If your business involves keeping parts or products in a warehouse, you will inevitably develop problems that cause delays in delivery, lost items, inaccurate counts and other issues. You can tighten up your warehouse operations by giving your system a bit of time and thought. Do a careful observation of your facility and how it functions. Then consider the following strategies for making your warehouse operations more cost-effective and time-efficient.
Utilizing Available Space
Logistic experts find that up to 50 percent or more of order hours are spent on traveling through the warehouse. Managing your warehouse space for maximum utilization is in every company’s interest. Research new products that can help you maximize space in your facility. Implementing a flexible and adaptive pallet rack system from a place like T.P. Supply Co, Inc. is an essential component of good warehouse space management and a good investment for your business.
Lean Inventory Principles
Lean inventory management implements strategies that are designed to reduce costs and improve quality of operations. Essential principles include having inventory on hand when customers need it, improving the flow of operations to ensure efficient movement of personnel, cost reduction and a decrease in waste, and finally, standardization of products and procedures to ensure uniform outcomes throughout the department. These principles can help all businesses improve their operations, save money and improve customer satisfaction.
Using Technologies That Improve Efficiency
Today’s technological advances offer many opportunities to streamline warehouse operations and save money, like never before. A quality warehouse management software program can help you to ensure you have stock on hand when it’s most needed, as well as reduce errors and manage returns with greater accuracy.
Voice-tasking technology can keep hands free and allow employees to manage tasks faster and with fewer errors. Radiofrequency systems can help produce more accurate counts and fewer shortfalls during receiving, order picking and restocking tasks.
Design a Pick Plan
A consistent and reliable pick plan is essential to keeping your warehouse efficiently. Having employees wandering through your plant daily, looking for tools and other supplies can shave significant amounts off your profit margin. Set up protocols for handling orders throughout the picking operation. Make it easy for your employees to follow the protocols by providing the paperwork, product identifications and material handling equipment they need to do the job quickly and correctly.
Storing inventory over the long term can create a variety of problems that can cost your company money and hamper your ability to serve customers promptly. You should review your system periodically to determine if changing conditions have caused bottlenecks and inefficiencies that slow down your warehouse operations. If your system is preventing high productivity, make the changes in equipment, technology, and training you need, to have your warehouse hum like a finely tuned machine.
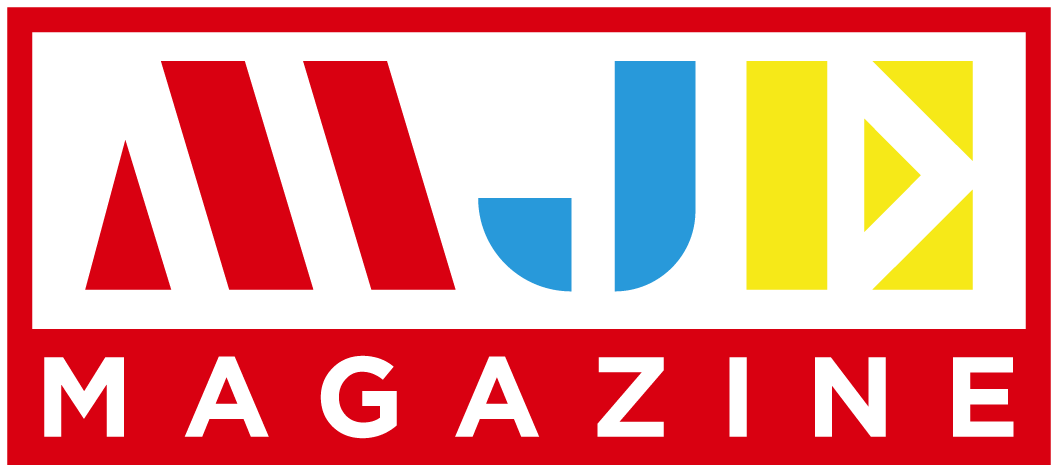